More durable than plywood, less expensive than steel: the new formwork system from alkus AG, the vacuum angle clamping device VWS, offers an economic alternative for the production of precast concrete components. Formwork elements consisting of alkus® solid plastic panels are fixed into position using vacuum – and can basically be located as required.
When alkus® solid plastic panels were launched more than ten years ago as an alternative to conventional plywood panels, scepticism towards the use of plastic was still widespread. However, due to their obvious advantages alkus® panels have since become an established form lining; for example alkus® AL with aluminium reinforcement and alkus® GM with glass fibre reinforcement for wall and slab formwork respectively. alkus® form lining GM 6 has also proved successful for curved formwork, in particular for tunnel construction and special formwork.
The critical success factors of alkus® panels are:
- perfect concrete surfaces without discolouration
- unprecedented longevity
- high-quality repairs with identical material
alkus® AL panels have been used successfully as formwork elements in the precast concrete industry for numerous years. alkus® panels are a highly efficient and cost-effective solution for between 50 and 300 uses – steel panels typically only achieve a worthwhile return on investment after roughly 300 uses.
Innovative formwork system that uses vacuum
True to its slogan, “Innovation Panel”, alkus® has always strived to develop and launch unique products. The first real innovation was the development of alkus® panels that can be repaired with identical material. This was followed by individual panels which can be welded together to create larger widths. Another unique feature is the 7-year long-term warranty on key technical properties.
The latest project focuses on precast concrete components. In this sector, construction of the respective form is a cost factor: until now formwork tables were either made from plywood or steel. The greatest disadvantage with plywood is its short service life caused by moisture penetrating through the nail holes. Steel panels are difficult to repair and demand the performance of complex cleaning tasks because of recurring rust problems. Steel formwork panels are usually fixed into position with a magnetic holder system.
In cooperation with J. Schmalz GmbH, alkus® has developed an economic alternative that uses vacuum technology. This system has been specially developed for formwork tables equipped with alkus® solid plastic panels. It allows formwork elements to be positioned as desired on the formwork table – without the need for screws, bolts or welding. The individual formwork elements are fitted with suction devices, and are connected via a hose to an air compressor that creates a vacuum. This ensures the quick, easy and safe production of elements in various designs and sizes.
Successful testing – pressure test with self-compacting concrete
The advantages of alkus® panels are key to the success of the new formwork system. The said formwork panels are easy to clean, can be repaired with identical material as well as welded together to create larger widths. Furthermore, alkus® solid plastic panels are easy to bend and cut to shape.
Precast concrete manufacturers therefore profit from an extremely economical and flexible solution. Initial tests have been very successful: it soon became clear that this system can withstand the pressure acting on the formwork from self-compacting concrete (SCC). The prototype has already been tested in real-life settings and will be showcased at bauma 2013.
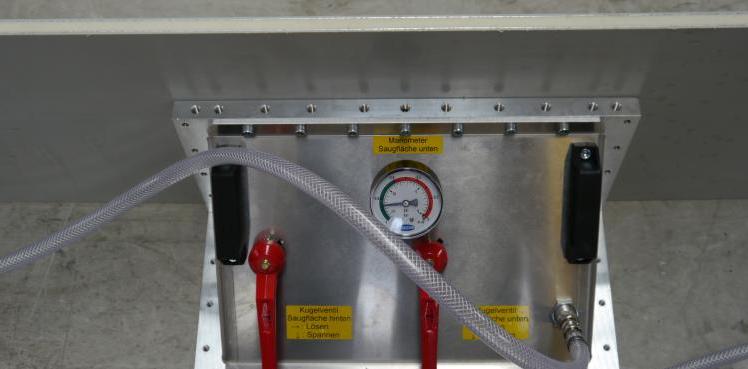
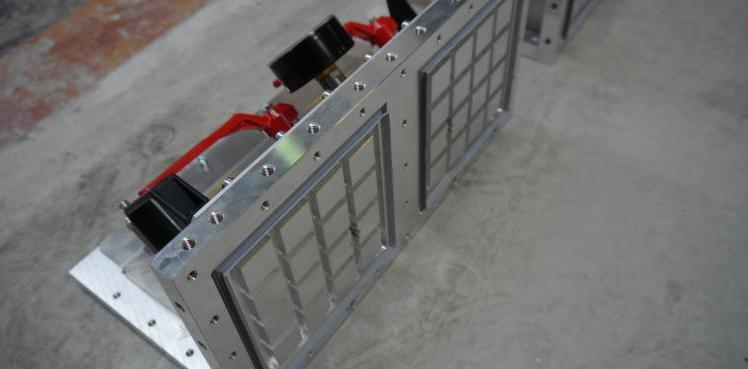
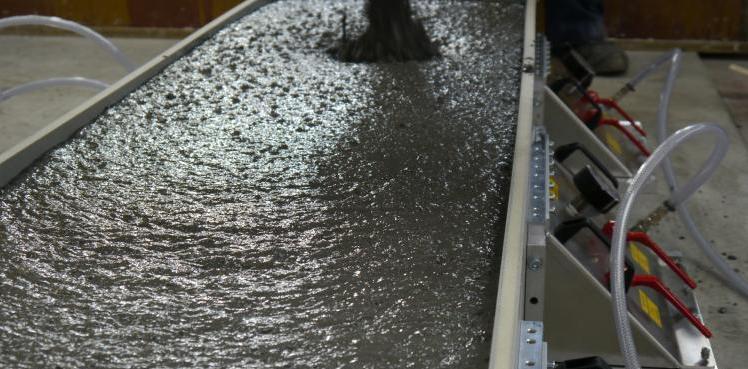
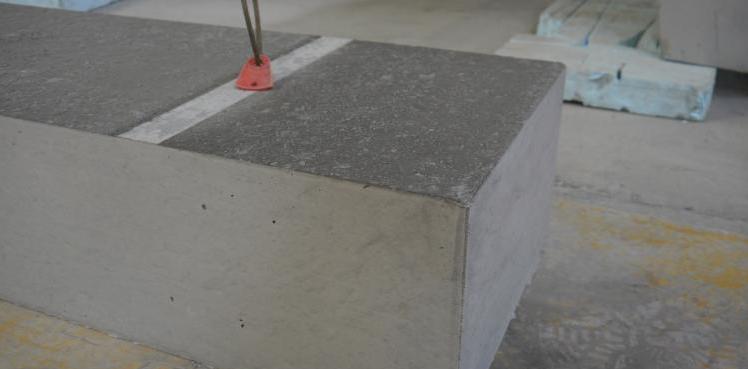