Re-panelling is an expensive and time consuming process, and nowhere is this more evident than in tunnel construction. Through the use of robust alkus® solid plastic panels, Huber & Sohn managed to cut costs and achieve better results during construction of the Blessberg Tunnel.
The 8314 m Blessberg Tunnel is the longest railway tunnel on the new Ebensfeld-Erfurt-Leipzig/Halle line and part of the German Unity Transport Project 8 Nuremberg-Berlin. It is intended to reduce the journey time between Munich and Berlin to just four hours from 2017 onwards. With a maximum depth of 330 m, the tunnel runs below the main ridge of the Thuringian Forest between Truckenthal and Goldisthal. A section of the famous Rennsteig hiking trail is located above the tunnel.
The joint venture “Blessberg Tunnel North”, consisting of the companies Ed Züblin AG and Bickhardt Bau AG, is responsible for the roughly 4000 m double tracked northern section and the required structures. As a subcontractor, Huber & Sohn was commissioned to construct nine tunnel enlargements, three turning points with a turning area and a connection to the main tunnel from the parallel running rescue tunnel.
Mobile formwork carriage with alkus® form lining
The formwork elements are prepared correctly at the factory. This has the advantage that the elements offer long-term dimensional stability. The 6 mm thick alkus® form lining GM 6 is used as the formwork panel for curved surfaces. Huber & Sohn has really good experience with this solution. The fibre glass reinforced solid plastic panels are extremely flexible and can be adapted easily to the respective radius – thus facilitating quick and simple installation. Furthermore, the panels are robust and durable. Solid plastic panels achieve much better results than timber panels without the need for complex and expensive re-panelling during tunnel construction.
In similar projects, Huber & Sohn had previously produced the walls first and then the ceilings due to the easier logistics. Working to an extremely tight schedule, the complete arch had to be formed and concreted in one process for six of the nine tunnel enlargements. Huber & Sohn therefore constructed a 10 m long mobile formwork carriage. The robust steel-timber construction can be separated for transportation.
“More effective and efficient with alkus® form lining”
The tunnel enlargements are roughly 20 m long. Assembly of the formwork carriage proved to be quite simple at the construction site. Once the concrete had cured sufficiently, the wall framework and the ceiling formwork were retracted and folded respectively. The formwork carriage, which can be separated in the middle, was subsequently rolled to the second concreting cycle. After concreting, the formwork was stripped and the two carriage parts were transported to the next tunnel enlargement. This method of construction ensured the six tunnel enlargements and a further six sections in the three turning points were completed on time. The formwork appeared to be as good as new after these 20 uses.
Ernst Flösser, the head of formwork, was extremely satisfied with the results: “The project manager confirmed that our concrete surfaces are comparable with the surfaces in the rescue tunnel that were constructed with steel formwork panels. The solution with alkus® form lining is, however, far more economical for our purposes. Even plywood form lining is too expensive due to the necessary re-panelling. The exact same panel has already been used over 70 times in previous projects.”
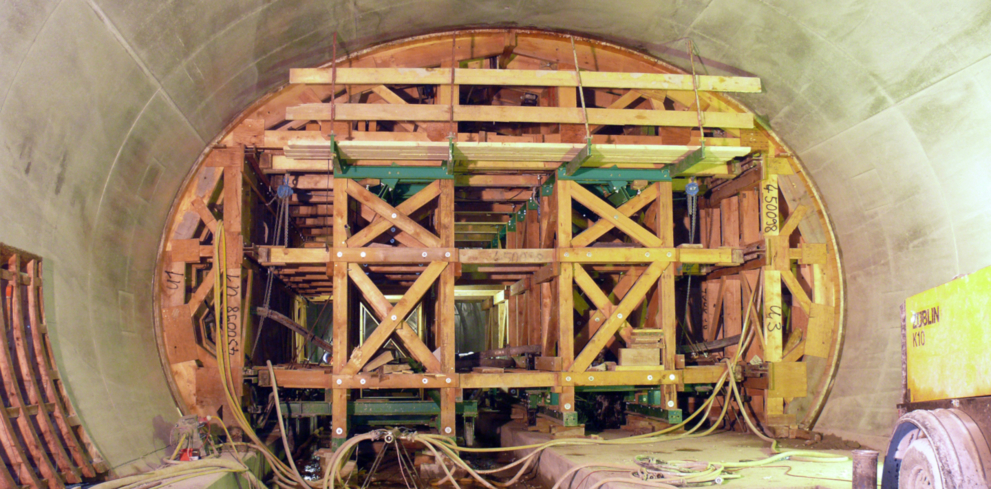
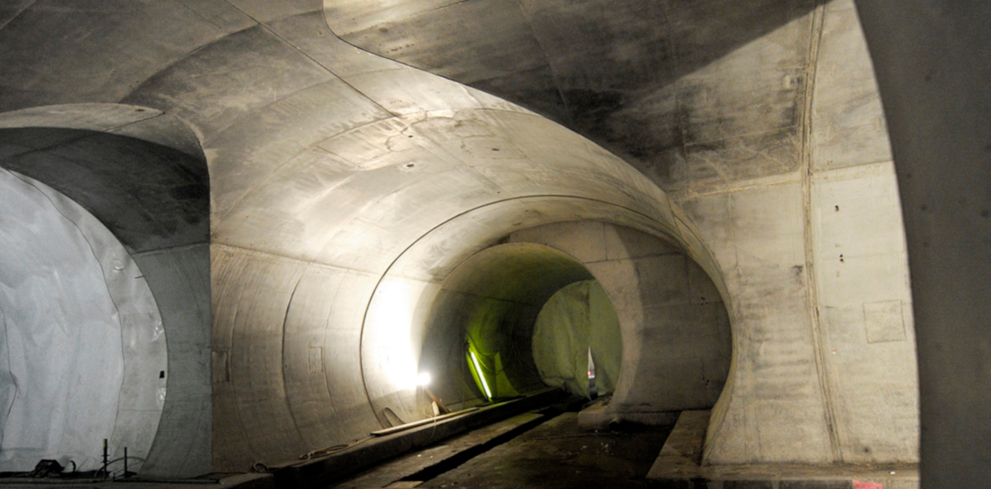