Award-winning: alkus repair process saves time, money and resources
With the alkus® solid plastic panel, scratches, holes – and even edges and corners – can be repaired in a matter of minutes thanks to a special repair process. This system solution makes the product particularly durable and sustainable, leading to it being named "Product of the Year 2024" by the readers of the German construction trade magazine "Baugewerbe". In the "Construction" category, it was awarded second place.
To ensure the alkus® solid plastic panel can be repaired using identical material, alkus has developed a unique welding device. It heats up and melts the alkus® welding wire, which is made of the same plastic material as the surface of the alkus® panel: polypropylene. The plastic is applied to scratches, holes and other damaged areas, sealing them immediately. After a brief cooling period, excess material is removed and the surface smoothed, ensuring the formwork panel is ready to go again. A slight deviation in colour is the only evidence of the prior damage, but this has no adverse impact on the concreting result: the panel is repaired without any loss of quality.
Guaranteed longevity
In addition to ensuring smooth concrete surfaces, this repair process also guarantees the longevity of the solid plastic panel. Instead of having to replace a damaged formwork panel with a new one, it can be repaired quickly and efficiently. It enables an alkus® formwork panel to be used more than 1,500 times. In contrast, a plywood panel must be completely replaced after roughly 50 uses. The alkus® panel is, therefore, a sustainable and cost-effective alternative for construction companies. Documented lifespans of more than 20 years confirm its long-term benefits.
Repairing large-scale damage
Even extensive defects do not necessarily mean that the whole alkus® formwork panel needs replacing, as the repair process enables the replacement of individual panel sections. This involves removing the damage to the alkus® panel with an electric router, cutting a suitable panel section to size and using it to replace the old one. The butt joints of the panel are then welded using the welding device and welding wire.
Repairing holes quickly
Holes measuring up to 4 cm in diameter can be repaired even more quickly with special polypropylene repair patches or plugs. To do so, a small repair patch or plug is tapped into an appropriately sized pre-drilled hole with a plastic hammer. The welding device is then used to weld around the edge of the repair plug. Finally, the surface is smoothed – the panel is thus repaired in just a few minutes.
Repairing edges and tie points
The edges and tie points of formwork panels can be damaged quite easily during daily construction activities. Luckily, their repair does not pose a challenge for us either. The panel edges can be reproduced using a special metal profile, which is modelled and attached to the defective edge and serves as the casting mould. The melted polypropylene is then used to fill the gap between the edge and the profile. The repair is complete once the surface has been smoothed with a scraper.
When repairing tie points, the cylindrical alkus® conical tube or alu-cone is used depending on the required diameter. This forms the mould for the tie point around which the polypropylene is then welded. Again, excess material is removed before smoothing the surface of the alkus® formwork panel. The result is smooth concrete surfaces without any gaps and holes.
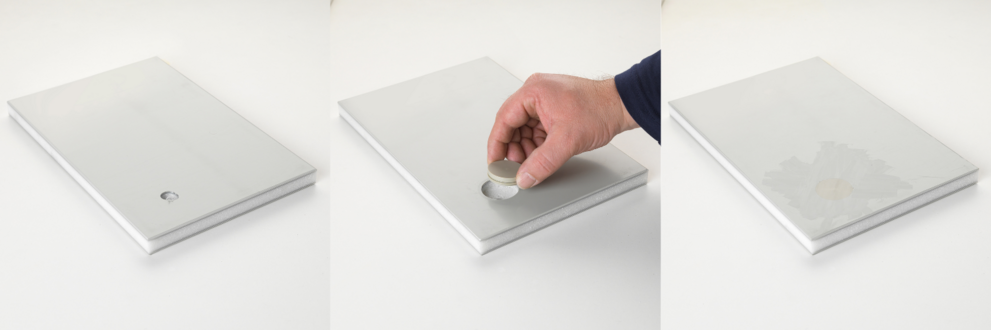
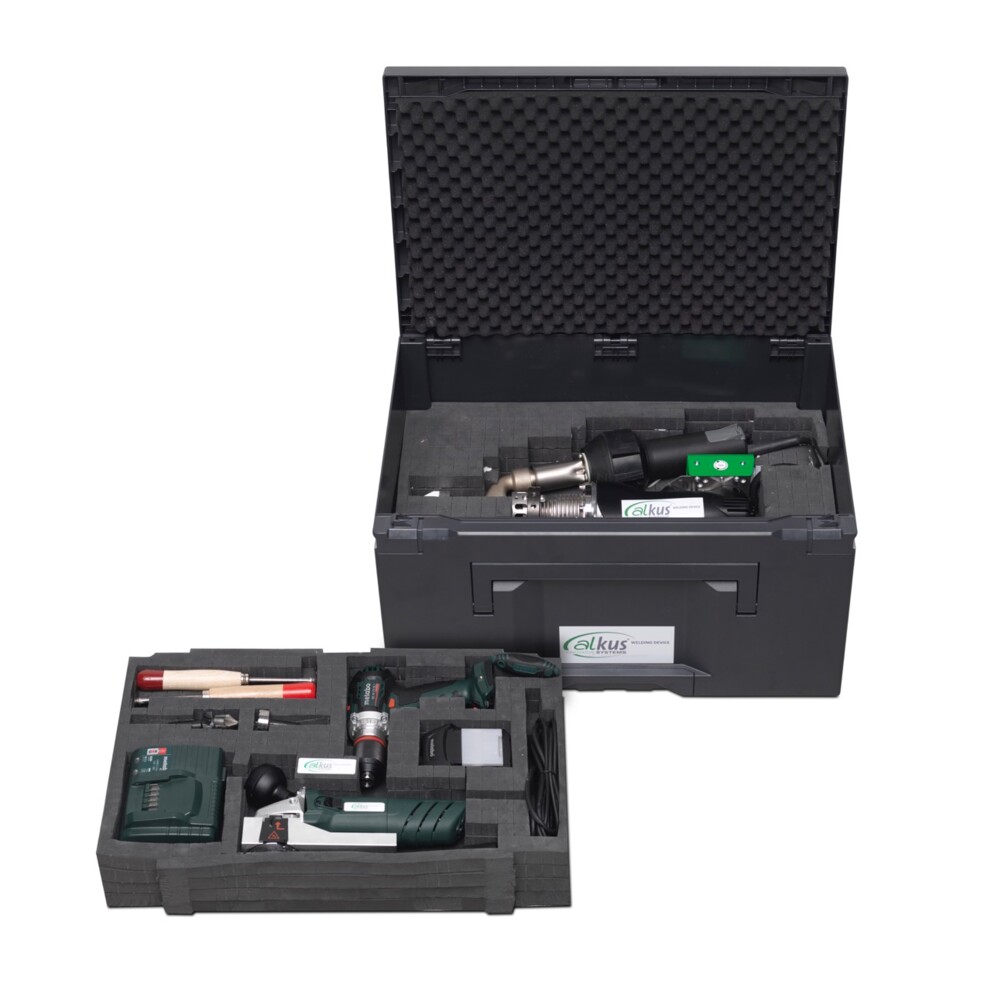
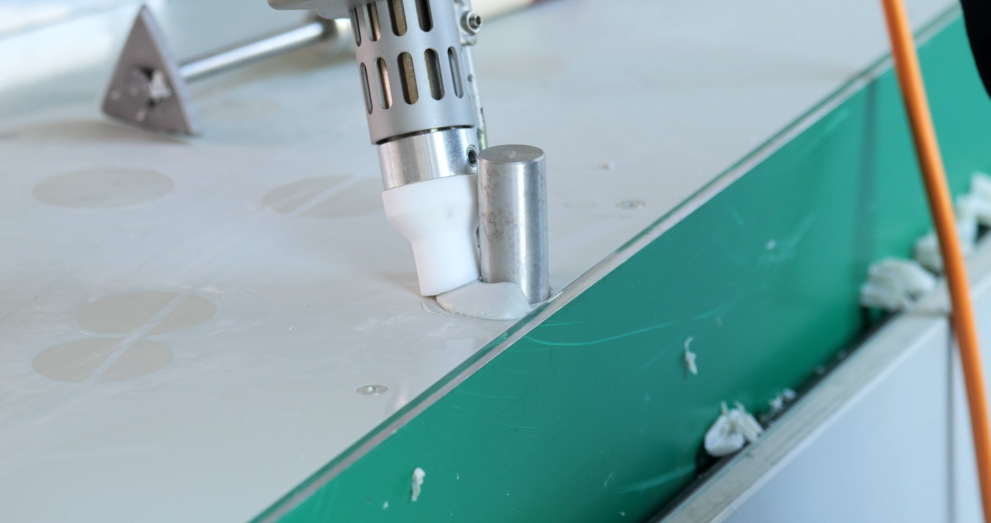