alkus® solid plastic panels have long since been used in precasting plants, as the advantages of reusable formwork are particularly relevant in this respect. However, when the precast units are 36-metre-long prestressed concrete trusses for a motorway bridge, the work involved is anything but normal, even for alkus AG.
In the summer of 2017, the Münsterland regional branch of Strassen.NRW - a state government enterprise tasked with planning, constructing and maintaining motorways and federal/state highways - began constructing a replacement bridge on the A30 motorway spanning the A1 motorway at junction Lotte/Osnabrück. This project is scheduled to run over a period of two years and incorporates several construction phases, including erection of a temporary bridge. Local firm Rekers Betonwerk GmbH & Co. KG based in Spelle was contracted to provide the T-beams (trusses) for the various bridge structures.
Needless to say, Rekers also had to tackle the problems facing all precasting plants: Steel is usually the material of choice for mass production formwork systems, while individual timber formwork, which is disposed of after use, is generally applied for single elements. Steel is too time-consuming and expensive for small and medium production runs, but timber offers limited dimensional stability and can be easily damaged, meaning several pieces of identical formwork are always required. “We had already had positive experiences with alkus® solid plastic panels and, therefore, also wanted to use them for this ambitious project,” explains Johannes Nitsche, head of process engineering at Rekers. In addition, there is no swelling or shrinking as the alkus® formwork panel does not absorb water. It, therefore, guarantees long-term dimensional stability and delivers optimum surface quality, even after being used many times.
100% waterproof thanks to sealed surface
The precast unit formwork was constructed for the prestressed concrete beams using 24 alkus® AL 20 panels with a total surface area measuring over 200 square metres. To guarantee the 36-metre formwork, the solid plastic panels were welded without a visible joint and finished with a sealed, rounded edge. “At our factory, we pre-fabricated three twelve-metre formwork panels for each side and attached them to the substructure directly at Rekers’ facility; in addition, the butt joints were welded at a distance of two millimetres without a visible joint,” says alkus specialist Michael Wagner. “The panels were supplied as straight alkus® panels and then bent accordingly by means of a pre-fitted V-shaped groove, thereby allowing us to achieve a sealed and thus fully water-resistant surface.” Each of the alkus® panels is equipped with roughly 53 holes with 120° countersink for secure attachment to the visible face of the supporting structure. The fixing holes were then sealed with identical material, making then invisible to the eye in the precast unit.
Thanks to the advanced services provided by alkus, it took just three days to fit the substructure with alkus® panels. The result: Outstanding exposed concrete quality for the entire small-scale series. The use of alkus® panels was therefore definitely worthwhile, even for a project boasting extreme dimensions: “All in all, the solid plastic panel is significantly cheaper for us than timber,” says Nitsche. “We only need to construct the formwork once, which obviously saves time and money when working with such large dimensions. Furthermore, we can store them outdoors.” This is particularly important as it is likely that months pass between the individual construction phases. Thanks to the alkus® lining, the formwork can then also be reused – at the same high quality.
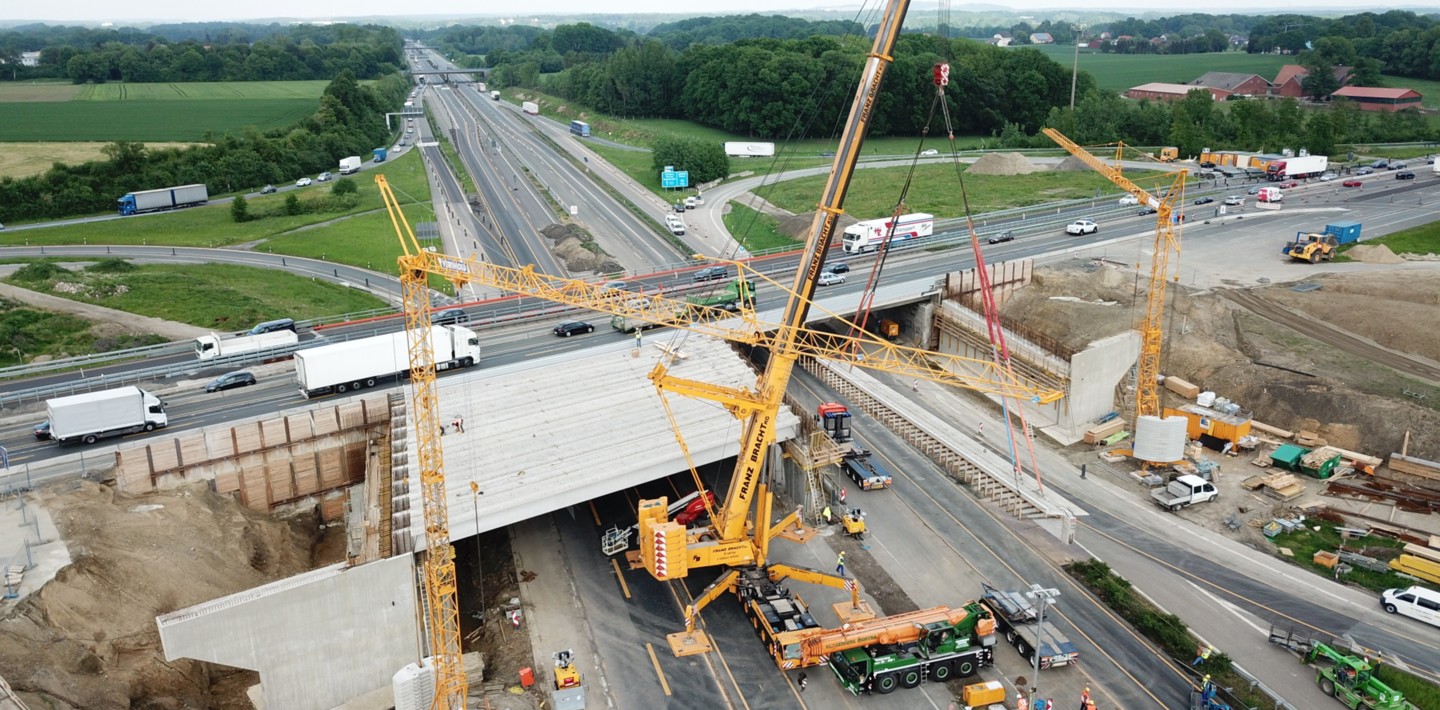
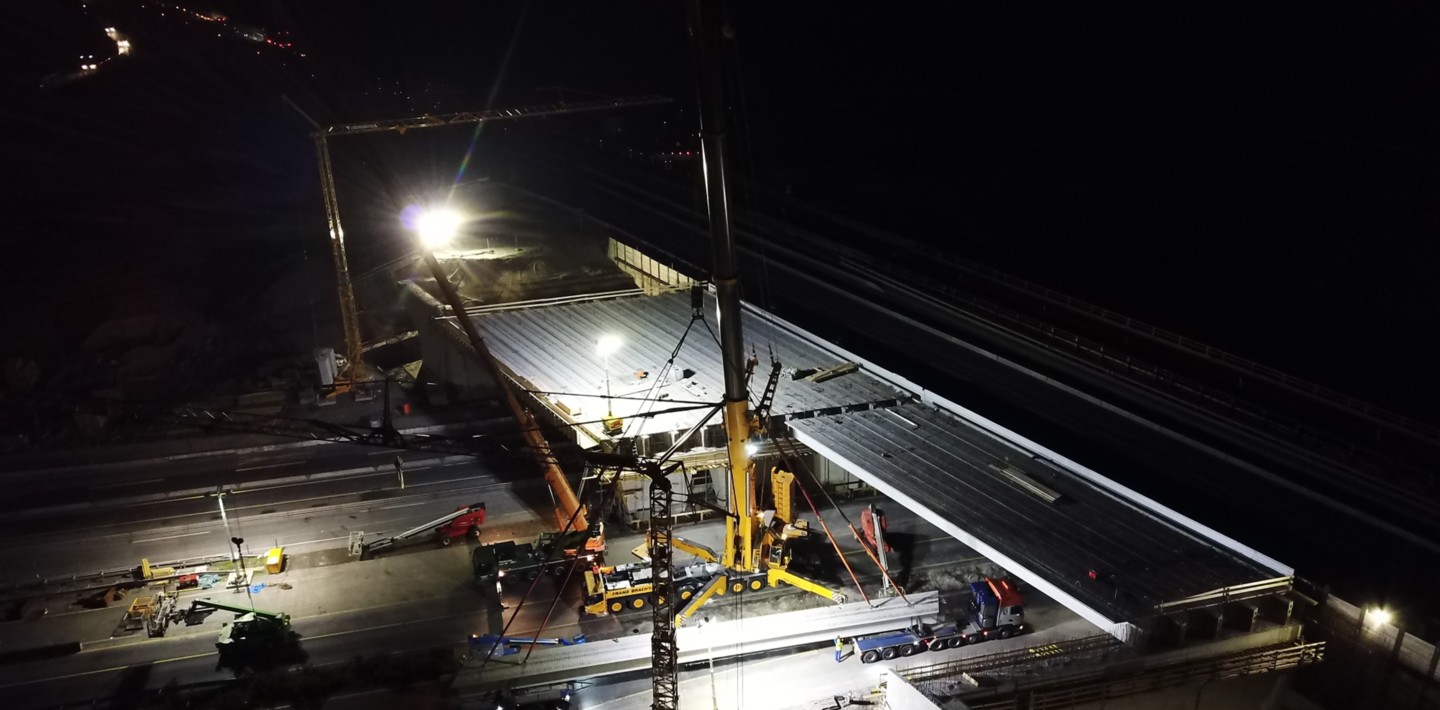
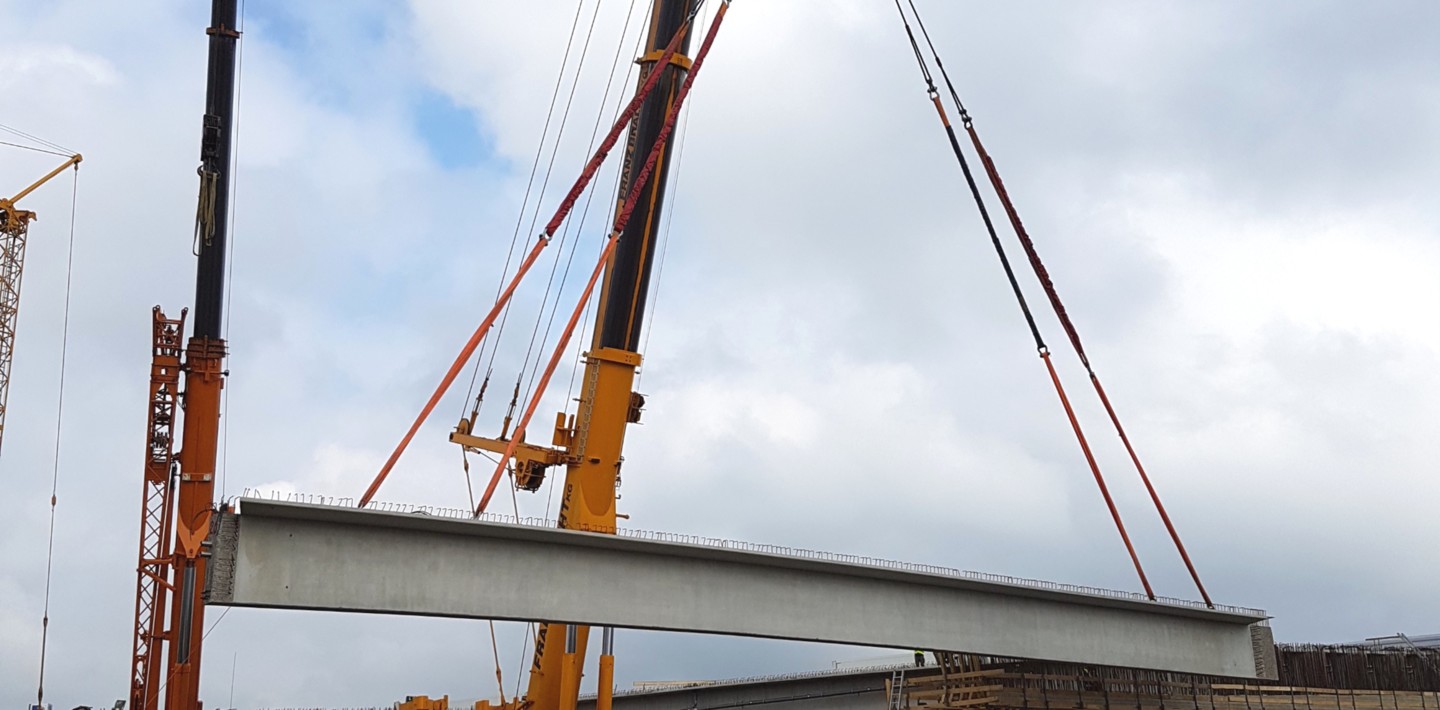