Construction of Swiss Life AG’s remarkable office and commercial building was commenced in Zurich in 2013 and concluded in 2015. The ensemble of three sections was named Tic, Tric, Trac – the German-language names for Walt Disney’s Huey, Dewey and Louie. The three buildings vary in size and number of floors. But a curtain-type wall made from finished exposed concrete sections was fitted to successfully create a uniform while eye-catching appearance in spite of these differences.
The Nägele company, which is a competent manufacturer of concrete finished parts and ready-mixed concrete that is based in Austria and Switzerland, was awarded the contract for these finished parts. It operates one of the most modern production facilities in Europe.
The invitation to tender bids for the project demanded more than 1000 finished parts in four different versions. The quantities specified were too small for expensive steel moulds. But too large for conventional timber moulds due to the limitations of wood. That’s because wood absorbs moisture and quickly begins to swell after several uses. This means that the parts made with it can’t be kept true to size and so become unusable. A maximum of 10 to 15 good parts may be produced with a new mould.
alkus® solid plastic panels were discovered as a possible alternative in the search for an economical solution that would fulfil the requirements; the apparent benefits and the expected large quantities that could be produced resulted in these panels being short-listed for use on the building. Subsequently, one-to-one mock-ups were made using formwork lined with alkus® panels to test their practicability. The results exceeded expectations and consequently it was decided to use the alkus® solid plastic panels.
Seamless finished parts with alkus®
The production of the sample mould already confirmed that the alkus® solid plastic panels are just as easy to work with as timber. Any transportable length may be produced because alkus® solid plastic panels are manufactured endlessly. It’s also possible to weld them together seamlessly along the width. That’s why the components’ maximum dimensions – in this case 8.05 m x 1.24 m – only play a limited role.
The project required the production of façade elements that were straight along their lengths but curved around the corners. This was where another benefit came into its own. alkus® solid plastic panels are easy to bend and shape so it was possible to create the curves and corners without loss of quality.
The detailed production planning was carried out and the number of required formwork components was optimised in close cooperation with alkus® technicians. The 1,150 finished parts were in the end manufactured with 13 formwork panels. This is the theoretical equivalent of 88 prefabricated parts for each formwork panel. The number of parts varied depending on the mould. For example, 130 high-quality parts were created from the round formwork section. These high volumes increased cost-effectiveness – and did so while maintaining the same finish from the first to the last concreting.
Production also revealed additional benefits. The alkus® solid plastic panels are not absorbent so they require less formwork oil. Furthermore less adhesion of the concrete reduces cleaning times.
And, as mentioned above, the quality of the finished parts did not vary from beginning to end. So Markus Achtelik, the production manager, was accordingly pleased. “We’re glad that we chose alkus®. All the mentioned benefits – that they’re more economical than steel and timber, for example, their durability, consistently good finish from the first to last component, absolute dimensional stability and so on – were realised. I also appreciated that the alkus® technicians provided their support with the formwork and shared their experiences with our personnel.”
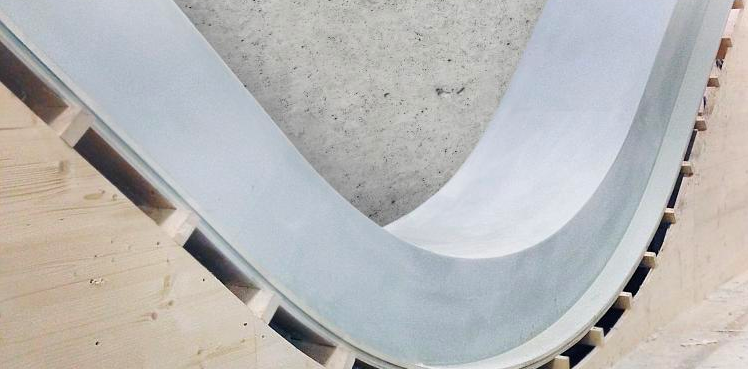
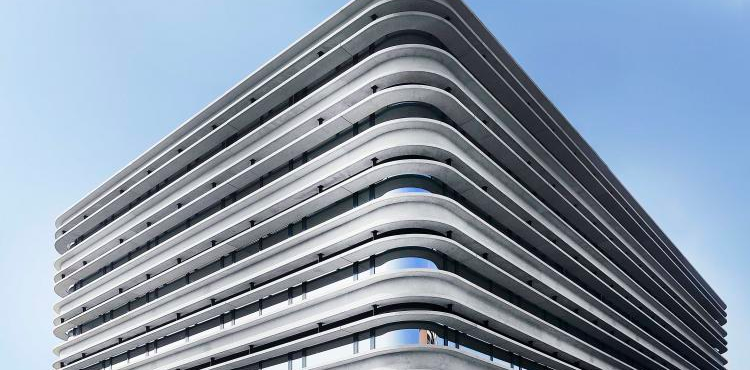
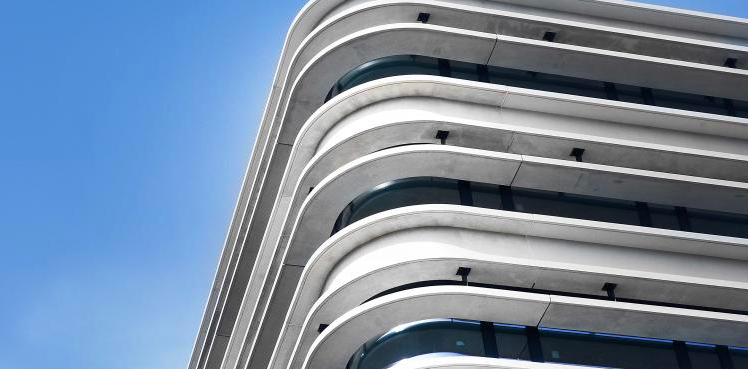